|
![]() |
現在、製造業や建築業では、CAD:Computer Aided Designというコンピュータを用いた設計が採用されています。さらに、CAE:Computer Aided Engineeringというコンピュータ上で行う物理実験(数値解析)を利用して、性能評価、最適化、品質向上などの様々な工学的な問題を検証しています。CAEはコンピュータ上で行う実験ですので、製品の形状や材質を、自由に何度でも変えることができます。また、実際に試作品や試験設備を作る必要もありません。このため、CAEを活用することによって、製作費や材料費をかけずに、さらに、短時間で繰り返し実験を行うことが可能となります。
さて、近年では特に「設計者CAE」という手法が注目を集めています。製品開発に携わる設計者自身がCAEを利用して、設計の問題点や改善点を特定し、その結果を自らの設計に反映します。これによって、より効率的に製品のコストや開発サイクルを削減し、品質を向上させることができるようになります。
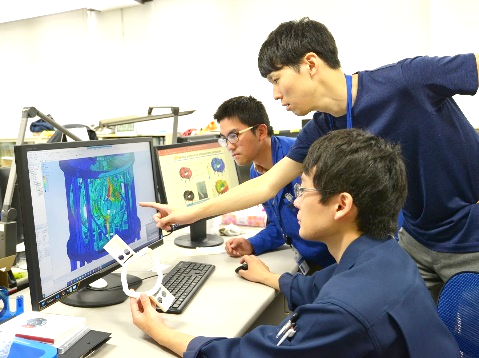
私は2000年代初めに、この「設計者CAE」という概念を知り、とても感動しました。もし設計者自らCAEを使い、設計の問題点や改善点を素早く検証できるようになれば、設計者はより多くの時間を、より自由な設計に投入できるようになる…これこそが、未来のエンジニアのあるべき姿ではないか、と考えました。
日本では古くから、勘と経験によって打開策を見つけ、度胸によってそれを実行することが尊重されてきましたが、設計において、この「勘・経験・度胸」による方法は、既存の知識に基づいて迅速に設計できるというメリットがある一方で、新たな解決策や効果的な設計案を見逃すといったデメリットもあります。
そこで私は、核融合研の数値解析環境を最大限活用して、従来の「勘・経験・度胸(K・K・D)」ではなく、「仮説・検証・データ(K・K・D)」による設計を実践することにしました。設計者が立てた仮設を、設計者自らCAEで検証して、そこで得られたデータに基づいて仲間と議論し、さらに良い設計を探求します(図1)。
さて、私は2011年から、「クライオポンプ」という真空ポンプの開発メンバーに加わりました。クライオポンプは高温プラズマの生成に必要な超高真空を実現する上で、不可欠な装置です。クライオポンプは、吸着材である活性炭をマイナス250℃という極低温に冷却すると様々なガスを吸着するという性質を利用して、ガスを排気する真空ポンプです(詳細はNIFS NEWSNo.236研究最前線をご覧ください)。ところが、極低温の活性炭は少しでも温度が上がると吸着性能が低下するため、クライオポンプは排気性能を失ってしまいます。そのため、壁を作って、高温のプラズマからやってくる熱が、出来るだけポンプ内部に入ってこないようにすることが大事です。とはいえ、熱の侵入を防ごうと、壁で囲いすぎると、今度は排気口が小さくなるので、これまたポンプ機能は低下してしまいます。したがって、クライオポンプは、「ポンプ内部への侵入熱は少なく」かつ「ポンプの排気口は大きく」という、一見、相反する設計要求をクリアしなければなりません。
クライオポンプの開発にあたり、まずはプロトタイプが製作されました。これは従来技術を基に設計され、水(約20℃)で冷却された水冷シールドと液体窒素(マイナス200℃)で冷却された窒素シールドの2つの熱シールドでポンプ内部への侵入熱を防いでいます(図2左)。その後、より高温のプラズマを実現するために、クライオポンプにも更に高い排気性能が求められるようになりました。私の仕事は、プロトタイプをベースに、クライオポンプを設計し直すことでした。はじめは、排気性能を高めようと、水冷シールドと液体窒素シールドの形状や大きさを変えるなど、思いついたアイデアを次々とCADを使って設計しては、CAEで解析を行いました。ところが、何度繰り返しても、ポンプの排気口が大きくなると、ポンプ内部への侵入熱も大きくなるばかりです。性能を良くするどころか、ポンプとして成立させることも難しい有様でした。そのうち、とうとうアイデアが尽き、一時はもう無理じゃないかと諦めかけました。
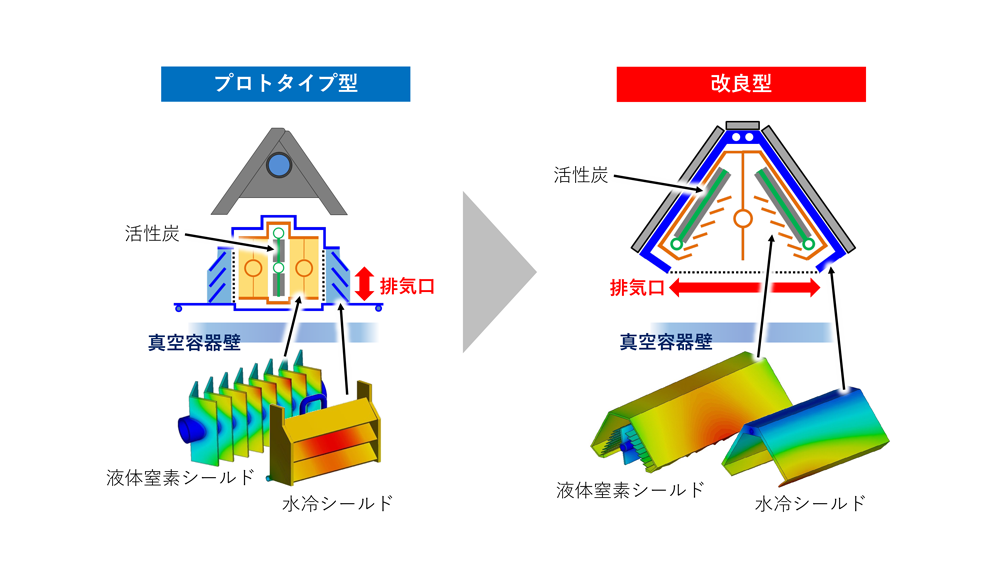
そんなあるとき、ふと、「吸気口の水冷シールドを無くしても、構造を工夫すれば侵入熱を抑えられるのではないか」と仮説を立ててみました。上述のように、従来のクライオポンプは2種類の熱シールドで構成されています。したがって、この水冷シールドを無くすという発想は、本来なら定石外のアイデアです。しかし、他に良い方法も思いつかないので、ものは試しと検証してみることにしました。この仮説に基づいて、いくつかモデルを作り、CAEを用いて解析を繰り返しました。また何度か試行錯誤するうちに、排気口を真空容器側に向けると、真空容器が水冷シールドの役割をして、結果としてポンプ内部に入る熱が少なくなることを発見しました。そこで図2右のような構造を考え、排気口を出来るだけ大きくしてみました。その結果、吸気口に水冷シールドが無いにも関わらず、プロトタイプに比べて、ポンプ内部への侵入熱は少なくなるという驚きの結果になりました。液晶モニターに映るそのデータを見た時は、驚きとともに大変興奮しました。
その後、この設計に基づいて作られたクライオポンプは2016年からLHD実験で使用され、現在も核融合研究に役立てられています。このように、CADによるモデリングやCAEによる数値解析を駆使しながら、何度も試行錯誤を繰り返し、新たな打開策を探求していく設計業務は、ときに挑戦的でありながらも、とても充実感のある仕事です。
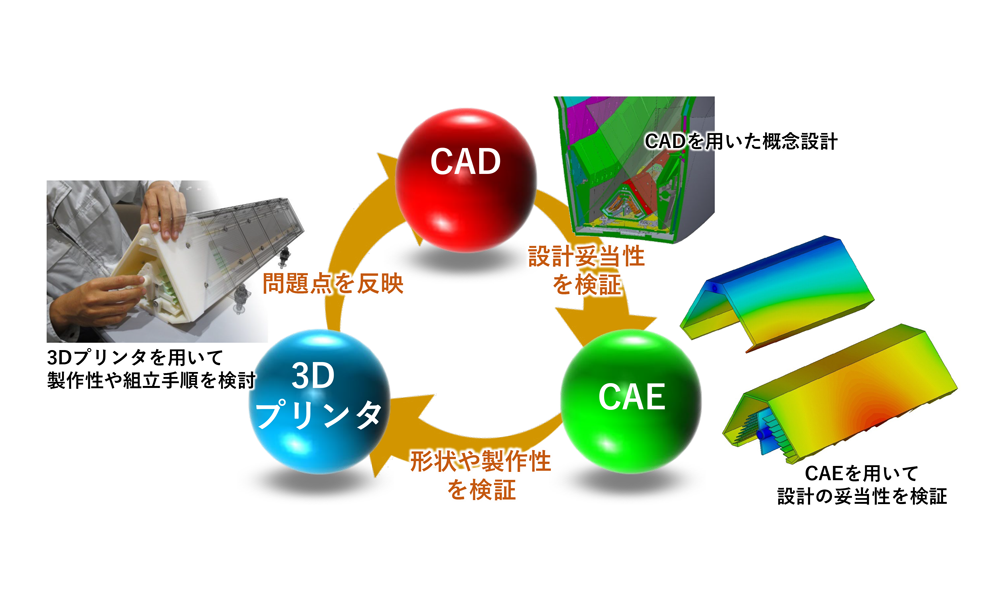
2017年頃から、技術部では、解析技術に関する人材育成にも力を入れるようになりました。いまや設計活動に欠かせなくなった、CADやCAEの基本ツールについてのセミナーや講習会を開催するとともに、毎年、大学研究機関の技術職員から参加者を募り、技術交流「有限要素法を用いた解析技術」を企画運営しています。これにより、CAEを用いた解析技術の普及や技術継承、情報共有や人的ネットワークの構築を目指しています。
また技術部では、立体物を出力することのできる3Dプリンタも設計に活用しています(図3)。設計の早い段階で、製作性や組み立て手順を確認できれば、後々問題になる不具合を事前に発見することができます。CADとCAEに加えて、この3Dプリンタを活用すれば、単に開発期間やコストを削減するだけでなく、高い設計要求に応える、より自由で高度な設計も期待できます。このほか、CAEの結果を直接3D造形して、設計に役立てる試みも行っています。通常、数値解析の結果はモニターで確認するか、紙に印刷して確認します。もし、図4のように、CAEの解析結果をそのまま3D造形することで、開発に関わる多くの人が直接手に取って確認できれば、より直感的に解析結果を捉えることができ、それにより、さらに良いアイデアを創出できるかもしれません。
今後も、CAEを活用した高度な設計、解析技術の普及活動、及び人材育成など様々な活動を通じて、より良い設計のあり方を追求するとともに、ますます活発になる核融合研究を支援できる人材になりたいと願っています。
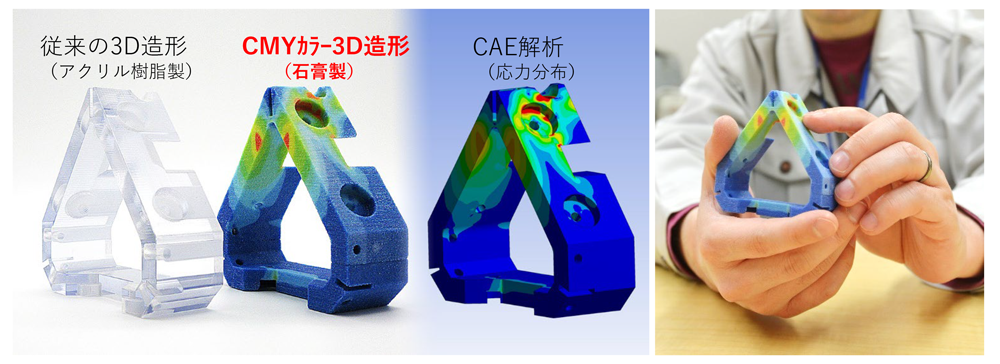
(技術部 設計開発技術課 技師)